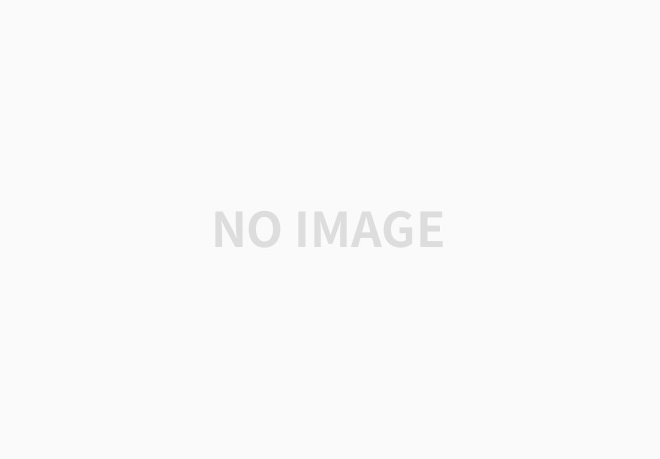
고분자 OLED는 일반적으로 양극으로는 ITO를 사용하죠. 그리고 이 위에 용액 공정으로 고분자 유기막들을 도포합니다. 유기막의 경우, 발광층 하나만으로도 작동은 가능하나 정공과 전하의 균형을 맞추어 발광 효율을 높이기 위해 전하들을 잘 전달하거나 혹은 발광층을 지나는 전자를 막아주기 위해 부가적인 유기막들을 삽입하여 대부분 두 층 이상의 유기막이 적용됩니다. 유기막들은 저분자 OLED와 유사하게 전하들의 주입층, 수송층, 저지층, 그리고 발광층들이 적용되는데, 보통 하나의 유기막이 복합적인 역할을 하는 경우가 많습니다. 다만, 고분자의 경우, 막의 형성 과정은 간단하나 분자 구조가 복잡하고 전하 균형을 맞추는 것이 만만치 않으며, 또한 정제 과정에서 불순물이 함유, 혹은 잔류될 소지가 높은 점, 그리고 막 형성시 상호 반응이나 섞임이 일어날 수 있다는 점 등이 고려되어 소자 설계가 이루어져야 합니다.
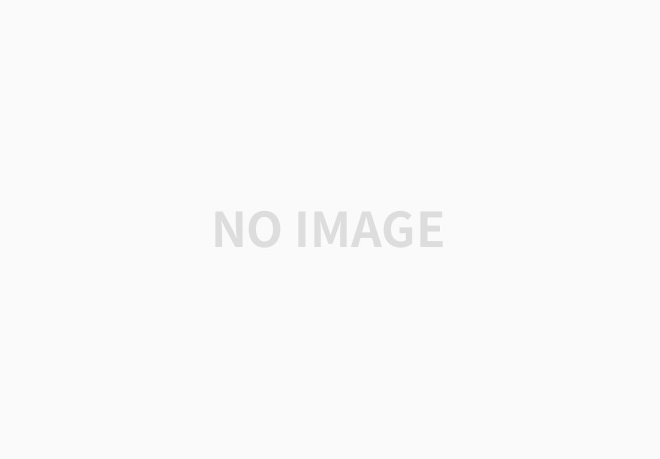
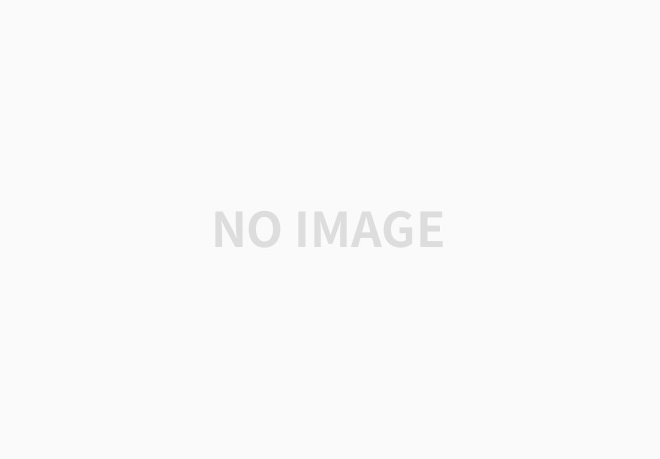
고분자 소재는 저분자에 비해 분자량이 만 배 이상이 커서 안정화되어 있으며, 따라서 진공 공정대신에 용액 공정이 가능하다는 점을 앞서 말한 바 있습니다. 따라서, 고분자 OLED의 경우, 저온 공정이 가능하고 전반적인 공정이 단순하며, 대면적에 유리한 특징을 가지고 있고, 재료의 사용 효율과 친환경적인 측면에서도 유리하고, 설비 투자와 제조 가격의 부담이 저분자 OLED에 비해 적습니다. 이에 더하여 구동 전압이 낮다는 특징도 있죠. 다만, 소재 합성 후 반응 촉매 등이 완전히 제거되지 못하여 소재의 순도가 떨어지고, 용액 공정 후 가열이나 열처리를 통해서도 용매나 반응 촉매들이 온전히 제거되지 못하여 오염에 취약하다는 단점이 있습니다. 이는 제작된 소자의 색순도나 효율, 수명 등이 저하되는 원인으로서 작동하죠. 이에 더하여 용액 공정의 특성상 유기층들간의 섞임이나 번짐, 그리고 화소 크기를 줄이는 데 제한이 있다는 등의 문제점들도 남아있습니다.
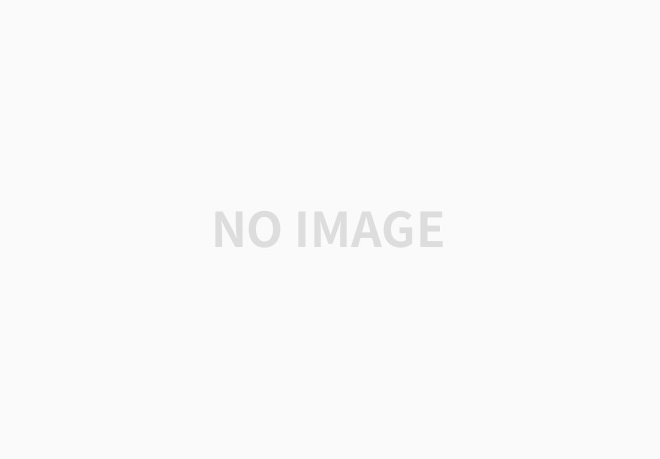
용액 공정을 좀 더 들여다보죠. 가장 흔한 용액 공정은 스핀 코팅이며, 이 외에도 그라비아 인쇄, 스크린 프린팅, 임프린팅, 그리고 노즐을 이용하는 잉크 젯 프린팅 등이 있지만 연속적인 막의 도포시 상호 반응 내지는 침투할 가능성이 높아 보통 2 ~ 3층 정도에서 소자를 완성합니다. 특히, 비접촉식이며, 원하는 위치로만 토출되므로 마스크 공정이 없이 패턴 형성이 가능하며, 버려지는 재료가 적어 재료 사용의 효율성이 높은 잉크 젯 프린팅 기술이 많은 주목을 받고 있는데, 이의 완성을 위해서는 높은 순도는 물론 일정 이상의 점도, 낮은 증기압 등을 특징으로 하는 잉크 소재의 개발과 함께 미세 패턴을 만들기 위한 연구 개발이 더 진행되어야 합니다. 고분자, 용액 공정을 통한 OLED는 적지 않은 어려움에도 불구하고 저온 공정, 생산성과 환경 등의 장점을 살리기 위해 지속적으로 연구 개발이 진행되고 있습니다.
# 참고로 하고 있는 여러 자료들의 제공에 감사를 표하며, 계속 업그레이드 됩니다.
# 의견과 조언, 수정과 요청은 늘 환영합니다. 댓글이나 전자메일로~ bkju@korea.ac.kr
# 저작자, 본 사이트를 반드시 표시, 비영리적으로만 사용할 수 있고, 내용 변경은 금지합니다.
# 더! 생각해보기
a. 고분자 OLED가 실용화되기 위해서는 어떤 약점들이 어떻게 해결되어야 할까
b. 고분자 OLED의 해상도는 어느 정도까지 가능할까. 그 근거는 무얼까
'공부와 생각들 > 디스플레이 공부' 카테고리의 다른 글
5-5) OLED, 분류, 배면 발광과 전면 발광 (0) | 2019.12.19 |
---|---|
5-4) OLED, 분류, 수동 구동과 능동 구동 (0) | 2019.12.17 |
5-2) OLED, 분류, 저분자와 고분자 (0) | 2019.12.12 |
5-1) OLED, 분류 (0) | 2019.12.10 |
쉬어가기) 박막 트랜지스터 (0) | 2019.12.06 |